Crumbling RAAC is just the tip of the iceberg according to UWE Bristol academic
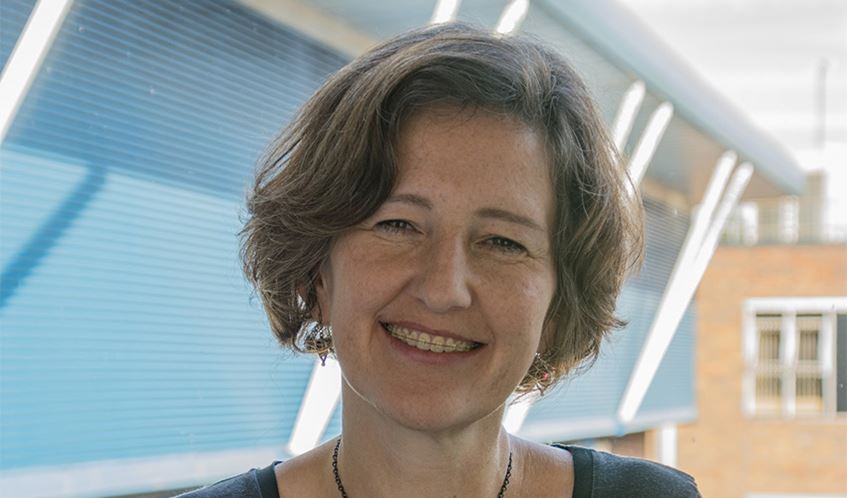
Alice Moncaster, Professor of Sustainable Construction, School of Architecture and Environment, UWE Bristol, shares her thoughts on this developing RAAC story:
“Crumbling schools are in the news, with hospitals following closely on their heels. But, this is not the result of shoddy design and construction in the last century. Instead, it is the canary in the coal mine – just one more indication of the perfect storm we are facing as a consequence of decisions which have led to a long-term lack of investment in infrastructure combined with a changing climate.
“My PhD was focused on school building projects, at the time of the last Labour Government’s ‘Building Schools for the Future’ (BSF). I found that there were many issues with bureaucracy and over-spending in BSF; however, the solution was not to axe the much-needed extra funding, as happened in 2010.
“So, what are these RAAC components which are suddenly being discussed? RAAC (as every news article will now tell you) stands for Reinforced Autoclaved Aerated Concrete. It is ‘bubbly’ concrete, reinforced with steel reinforcement bars, and cast in factories into concrete planks or panels, for use in roof structures, and sometimes floors or walls. It is therefore a form of ‘MMC’ - modern methods of construction (although the ‘modern’ is debatable). Really this just means large components made offsite in a factory rather than concrete being poured in situ. If you want to know more, do read the CROSS explanatory page here.
“It's important to stress that RAAC was used in public buildings such as schools and hospitals because it was a) quick to construct and b) low-cost. As with other forms of MMC, RAAC doesn’t require shuttering to be formed on site, then steel reinforcement cages to be constructed, and then wet concrete to be poured, then left to ‘cure’ for several weeks. All of those processes have happened in the factory already, and the material is ready to use, making it a far quicker construction process. RAAC was also cheaper than alternatives, partly because it took less time to build and ‘time is money’ in construction, and partly because the bubbles of air meant it used less cement, the most expensive part of concrete. These are still important factors in choosing construction materials, particularly for buildings built with taxpayers’ money. In addition, it is becomingly increasingly evident that there is a third issue, c) the greenhouse gas impacts (‘embodied carbon’) of the material, which is even more critical. RAAC wins on that one too – because it has bubbles of air, there is less cement, and cement is a carbon-intensive building material.
“So, we can’t blame the architects and engineers of the last century for using a material which appeared – and still appears - to tick all the boxes.
“So why is RAAC now crumbling? There are several things are going on here:
“A process called carbonation is partly to blame: this affects all concrete, and is a process where it gradually re-absorbs carbon dioxide from the air at exposed surfaces, reducing the pH and leading to a higher risk of corrosion of reinforcement. Even though RAAC has coated reinforcement, air bubbles mean it is much more likely to be near an exposed surface. RAAC is only used on internal structural elements, rather than external cladding, for this reason.
“As with any manufactured material, RAAC will also have had a ‘design life’, beyond which it would be expected to be replaced or at least to need considerable maintenance. That design life has now come to an end. But few school buildings have been replaced since BSF, and for many years roofs and external cladding have been poorly maintained, leading to opportunities for rain to get in to the internal structural elements, and cause long-term damp problems. This will be exacerbating the risk of corrosion in any reinforced concrete elements, not just aerated ones.
“On top of that we have a changing climate to deal with. Last winter in particular saw exceptionally heavy rainfalls across much of the UK, with driving rain leading to increased failures of roofs and cladding systems. In addition, increased droughts, such as that from last summer, have led to ground shrinking and foundations moving, causing the building structures above to crack. Schools – as with all buildings - will have been designed to meet building codes which were based on the expected weather of their era, and in their location – a school in the North West of Scotland will have been built to withstand heavier rainfall than one in the South East of England for example - but none will have been built to withstand last winter’s weather, or that we can expect over the coming years.
“Finally, a known problem with concrete is that it fails suddenly and without warning. While materials in tension, such as timber, are more likely to fail gradually by bending (see for example many old Tudor timber-framed houses), materials like concrete which are brittle will fail catastrophically, and with potentially devastating results for the building and anyone in it.
“And yes this is likely to happen to hospital buildings too, for exactly the same reasons.
“What can we do about this, as the AEC (Architecture-Engineering-Construction) professions? It is clear that there are immediate roles for building surveyors to assess the condition of existing buildings, and for structural engineers to design rapid temporary support structures. But it is also clear that we need to educate our future professionals to understand the much wider picture in which their buildings will be used. This story is one of politics, and of climate science, as much as it is of structural calculations. We need design teams and architects who can understand every aspect of a building, throughout its life. We need services engineers who understand how to minimise energy use in a building, and structural engineers who can design with low embodied carbon materials; but they also need to understand how that building will be used and maintained in the future, and what that means for its wider sustainability. Finally, as embodied carbon calculations demonstrate repeatedly that replacing buildings is more carbon intensive than retrofitting them, as an industry we need to embrace the least sexy but most important role going forwards – how to retrofit our existing buildings for future climates.”
Related news
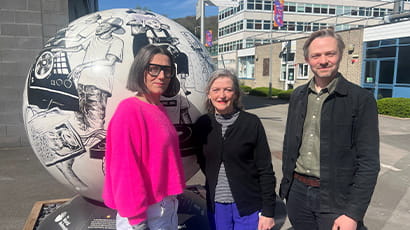
09 April 2025
UWE Bristol academics shaping the future of design across disciplines
Three senior leaders from the College of Arts, Technology and Environment have been appointed to prominent national roles in architecture, art and design.
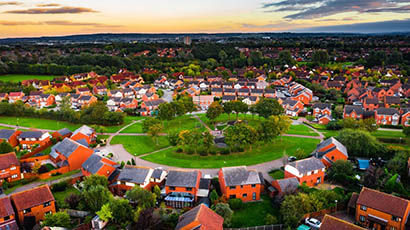
22 January 2025
Can DIY greening solutions transform your street and combat climate change?
Do-it-yourself (DIY) greening kits could help safeguard the country's most vulnerable communities from the impacts of a rapidly changing environment, according to a new project supported by UWE Bristol.
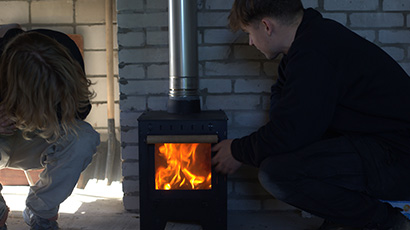
11 December 2024
UWE Bristol alum develops flatpack wood stove to heat homes damaged in conflict
A UWE Bristol alum has designed a flatpack wood burning stove which will provide a vital heat source for people whose homes have been damaged in areas of conflict across the world.

09 December 2024
UWE Bristol architecture students return from ‘once in a lifetime’ bamboo pavilion build in Ethiopia
UWE Bristol architecture students travelled to Ethiopia where they designed and constructed a large-scale bamboo pavilion in a park close to the capital city.
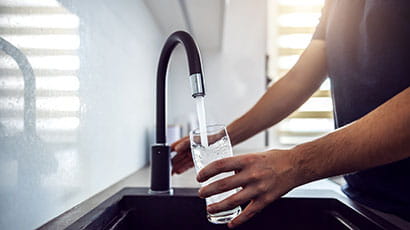
29 August 2024
Public trust in drinking water safety is low globally, study finds
A new study has found more than half of adults surveyed worldwide expect to be seriously harmed by their water within the next two years.
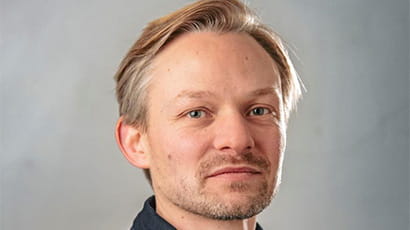
07 June 2024
Academic selected as Design Council Expert
Dr Matthew Jones has been selected to join the new cohort of Design Council Experts.
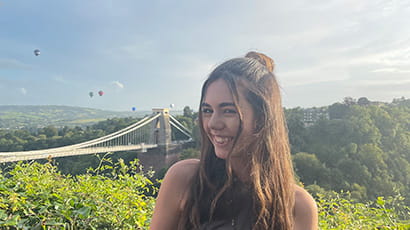
04 June 2024
Urban places and spaces should be accessible for all, says UWE Bristol student
Student Emily Annakin is hoping to land her dream job, using her own experience of visual impairment to design inclusive urban spaces.
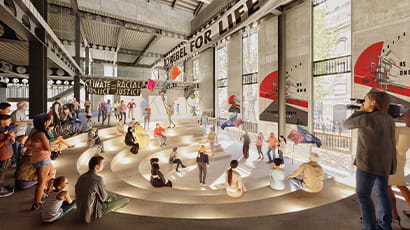
07 May 2024
Graduating students gear up to present their work at annual Showcase
UWE Bristol's Showcase offers visitors the chance to discover a new generation of talent from the College of Arts, Technology and Environment.
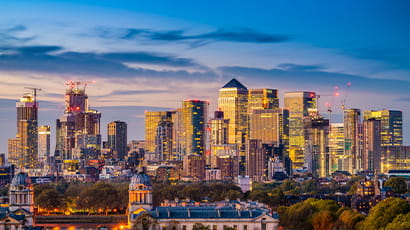
26 March 2024
Architecture must change beyond recognition to meet the climate challenge
A UWE Bristol professor is leading a new campaign which calls for a radical change across the built environment sector.
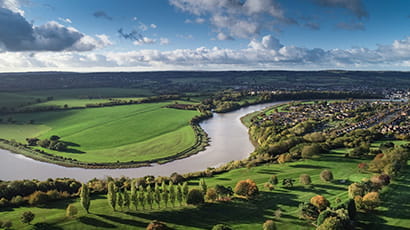
13 March 2024
Funding awarded to UWE Bristol to monitor the health of UK rivers
UWE Bristol is to receive a share of an initial £7 million investment to improve capability for monitoring the natural environment.
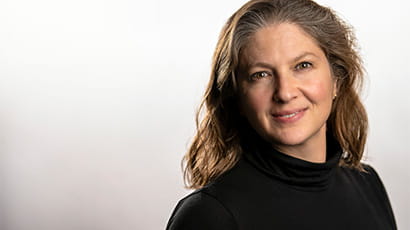
05 February 2024
UWE Bristol appoints professor to lead sustainability work
Dr Georgina Gough Professor for Education for Sustainable Development is one of only three professors in the UK with this remit.
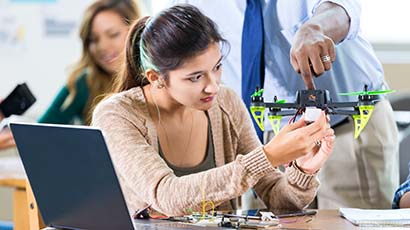
18 January 2024
Funding awarded to UWE Bristol to boost female participation in engineering and construction industries
UWE Bristol will increase numbers of women on engineering and construction degree apprenticeship courses to address industry underrepresentation, supported by funding from the Office for Students (OfS).
You may also be interested in
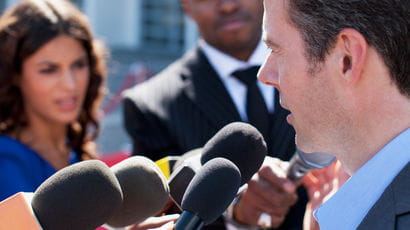
Media enquiries
Enquiries related to news releases and press and contacts for the media team.
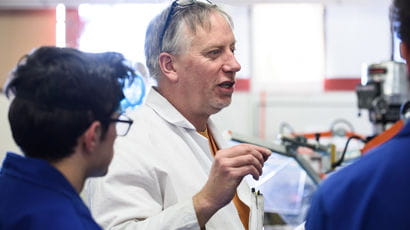
Find an expert
Media contacts are invited to check out the vast range of subjects where UWE Bristol can offer up expert commentary.